ISO 9001 Design Verification vs Design Validation
Table Of Content

You’ll be able to easily navigate between test reports and protocols to your design control verifications and validations, while also seeing related design inputs, risk controls, and components. The sooner you begin thinking about how you’ll verify these design inputs, the smoother the actual verification process will go. In fact, you should be considering how you’ll verify your design inputs while you’re defining them. If you don’t have plans in place for verification and validation, you’ll end up wasting an enormous amount of time on these steps, and you may miss key activities that could hold up your regulatory timeline. As with design inputs, be sure that your user needs are clearly defined at the beginning of the design and development process. For example, if one of the user needs is that “the device needs to be safe,” how will you validate that?
Electrical Engineer, E-2 Development
Product requirements (often included in a product requirements document) for our user need might look like below. Basically, in design validation, we need to demonstrate that the product meets the user’s needs. By the end of the process, you should have a list of design inputs and verification tests for each that will demonstrate that the device does what you intend it to do. More often than not, design verification involves suites of tests and trials. However, there are other acceptable verification activities, such as inspection and analysis (for a more extensive list of activities, refer to page 30 of the FDA Design Control Guidance). In this episode of the Global Medical Device podcast, we delve into everything related to design verification and validation, which is often called V&V.
Common Pitfalls in Design Validation
Conduct tests according to the plans you made in the preparation phase. Stay ahead 🪄 by getting introduced to new handpicked 🤖 AI tools 1x a week. This presentation starts with the introduction of our FPGA-based SoC control system DUT and testbench, then discusses advantages and disadvantages of using Vivado and Questa Core for verification. Learn how Allegro MicroSystems leveraged AI-powered Solido Design Environment and Analog FastSPICE to accelerate PMIC verification, resulting in an overall 5X reduction in verification time.
Process any number of images
By the way, the table above also shows the traceability between user needs and test cases. This trace matrix provides part of the V&V evidence that the FDA requires. Join 200,000+ other medical device professionals outperforming their peers.
As briefly mentioned in the design validation process outline, goals need to be specific and measurable. In the shopping cart example, a SMART objective would be to lower the number of users that abandon their cart by 9% within the next business quarter. Through design validation, you can ensure a user-friendly design that is meaningful for both the users and the business.
New Wave Design and Verification appoints Ike Song to Advisory Committee - Aerospace Testing International
New Wave Design and Verification appoints Ike Song to Advisory Committee.
Posted: Tue, 18 Jul 2023 07:00:00 GMT [source]
These are both essential aspects of ensuring the medical device can be used safely and effectively. ISO 9001 Design Verification and Design Validation are two steps that are distinctly different, and important in a good design process. Verification is used to make sure that the design has addressed every requirement, while validation is used to prove that the design can meet the requirements set out for it. You need to adapt the design verification and validation process to the needs of different industries. Design validation involves testing a product to meet the users’ precise requirements.
No matter when in the product lifecycle you make the change, you can’t skip verification and validation. Even in mid- and post-market stages, before and after product updates, you have to be ready to verify and validate. Planning and executing design verification and validation requires a deep understanding of the relationships between design controls. And if you’re using a paper-based QMS to keep track of all your work, it’s impossible to step back and see the full picture. This will often require more testing that will be used on production models. To ensure that all requirements are met, a full set of measurement and tests is done on the validation unit.
Specific FDA Requirements for Design Verification and Design Validation Activities
Skipping the design validation stage can hurt your UX design process and hence your final design outcome. The medical device development tools you choose should add to the accuracy and effectiveness of the work your team is doing, and not add unnecessary overhead to their daily tasks. A good tool provides guard rails to ensure that the important things are always done.
Previous PostNew Draft Guidance: How It Affects FDA 510(k) Submissions
He also served in various project management roles and has led global, cross-functional development teams for a wide variety of programs. During this time, he developed several award-winning and patented product designs. Greg holds bachelor and master of science degrees in mechanical engineering from the Georgia Institute of Technology.
Jesseca Lyons is a Senior Medical Device Guru at Greenlight Guru and a Mechanical Engineer by trade who loves working with cross functional teams, including both engineering and non-engineering disciplines. She’s spent most of her career gathering and defining requirements for new product design and development in the... We talk to a familiar guest and medical device expert Michael Drues Ph.D., president of Vascular Sciences.
Validation Package – A collection of documents produced during a validation project. Specification – A document outlining the requirements for a system or component. Quality Assurance – Team members tasked with ensuring product quality or process integrity. Deliverable – An obligatory object produced as a result of project execution, usually documents in validation efforts.
Stanley Electric Selects Siemens' Questa Advanced Verification Platform for its Newest MEMS IC Design - I-Connect007
Stanley Electric Selects Siemens' Questa Advanced Verification Platform for its Newest MEMS IC Design.
Posted: Wed, 11 Oct 2023 07:00:00 GMT [source]
Like any tool, it takes training and practice to gain the full benefit of the DVP&R. Once fully implemented into your company’s culture you will soon begin to realize the benefits. If you develop products — medical devices, particularly — then you’ve heard the terms and design verification and validation (also called V&V).
Design validation can be a complex process so having a plan is crucial. The design validation plan is a step-by-step approach to conducting a thorough design validation serving as the roadmap for the validation process. Heuristic evaluation is another useful method when it comes to conducting design validation. Heuristic evaluations are a great way to assess your design against established usability heuristics and uncover issues that might cause friction for our users. It takes much less maintenance effort to maintain traceability as your requirements, designs, and tests evolve than it does to patch critical holes in design and development at the 11th hour.
There’s no need to wait until you reach the validation step to start thinking about it. Whatever the case, your design verification activities are intended to prove that you’ve met the requirements of your design inputs. And that’s why the foundation of an effective verification testing process is well-defined design inputs. Greenlight Guru’s QMS solution features a dedicated Design Control Software workflow built specifically for medical devices. We understand the challenges of the design and development process, which is why with our software you can create detailed design control objects, link complex configurations, and attach documents with one click.
Verification – confirmation by examination and provision of objective evidence that specified requirements have been fulfilled. Traceability – The ability to ensure that requirements outlined in the specifications have been tested. Qualification – A testing protocol designating that a system meets a defined collection of requirements. Test plan, test cases, test execution records, and test results should be documented and maintained as a part of design records.
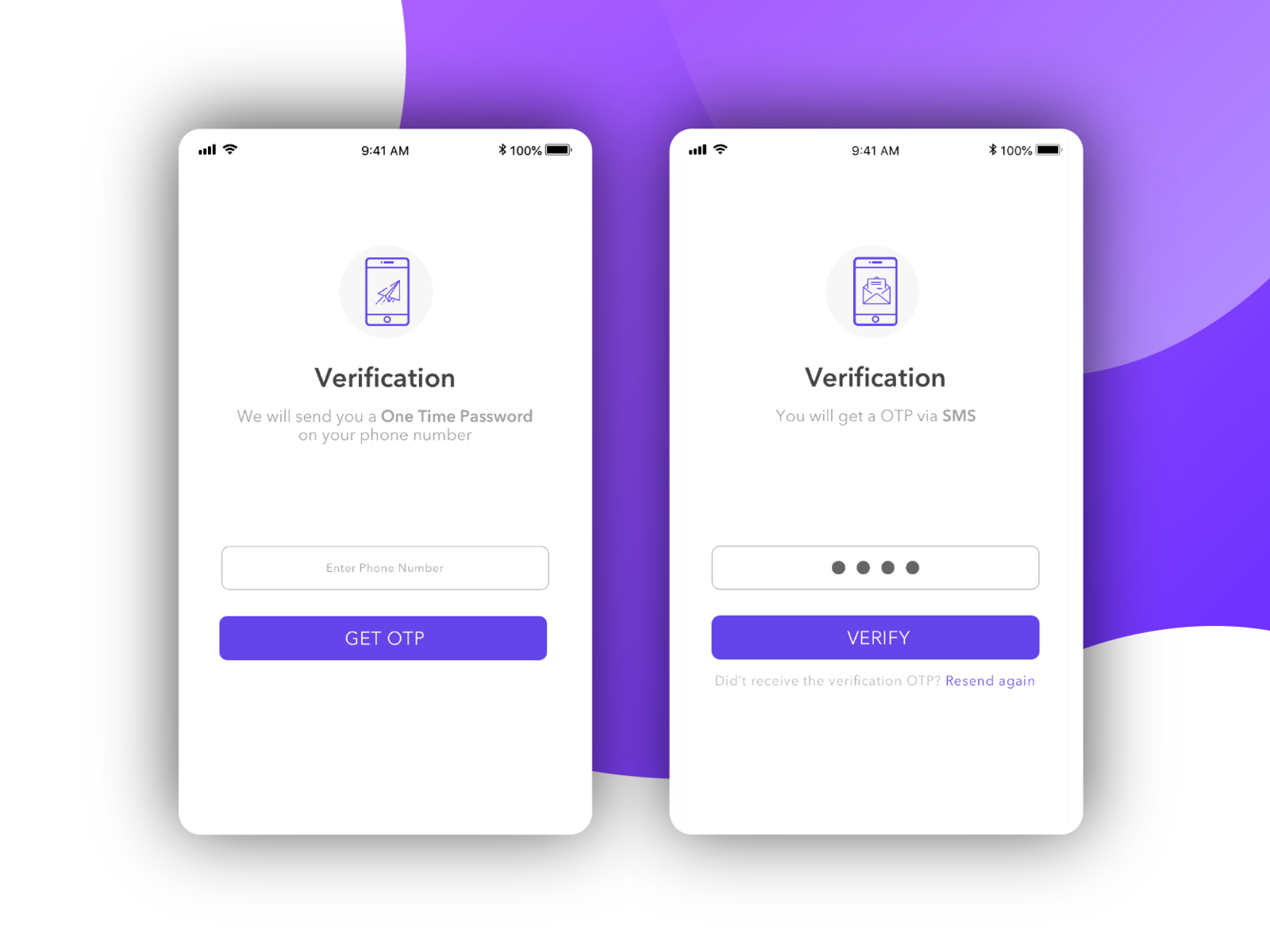
Design input is any physical and performance requirement that is used as the basis for designing purpose. Design output is the result of each design phase and at the end of total design effort. Validation is concerned with demonstrating the consistency and completeness of design with respect to the user needs.
Comments
Post a Comment